在现代工业生产中,
气动蒸汽调节阀作为控制流体流量的关键设备,其性能的稳定性和可靠性直接关系到整个系统的安全运行和生产效率。特别是在高温高压的异常工况下,对气动蒸汽调节阀的材料、结构设计以及制造工艺提出了更为严苛的要求。本文将深入探讨该设备在高温高压环境下的可靠性研究,分析其面临的挑战,并提出相应的解决方案。
一、高温高压环境的挑战
高温高压环境对调节阀的挑战主要体现在材料性能退化、密封性降低以及机械应力增加等方面。首先,高温会导致金属材料的力学性能下降,如强度减弱、塑性变形增大,进而影响阀门的使用寿命。其次,高压状态要求阀门具有较高的密封性能,以防止蒸汽泄漏,而高温会加速密封材料的老化,增加泄漏风险。最后,持续的高压还会对阀门的机械结构造成额外的应力,可能引发疲劳断裂。
二、材料选择与优化
针对上述挑战,选择合适的材料是提高调节阀在高温高压环境下可靠性的第一步。通常,高温合金如不锈钢、镍基合金因其良好的耐热性和抗腐蚀性成为常见选择。对于密封件,需要采用耐高温、耐蒸汽腐蚀的高性能材料,如聚四氟乙烯(PTFE)包覆的石墨或柔性graphite。此外,对关键部件进行特殊处理,如表面硬化、涂层防护等,也是增强材料性能的有效手段。
三、结构设计与创新
合理的结构设计能够有效缓解高温高压带来的负面影响。例如,采用压力自平衡结构可以减少阀芯所承受的压力差,从而减轻机械应力,延长使用寿命。同时,优化流道设计,减少流体阻力和涡流产生,不仅能够提高调节精度,还能减少因局部过热导致的材料损伤。此外,设置适当的散热结构,如翅片状外壳,可以有效提升热交换效率,降低阀门本体温度。
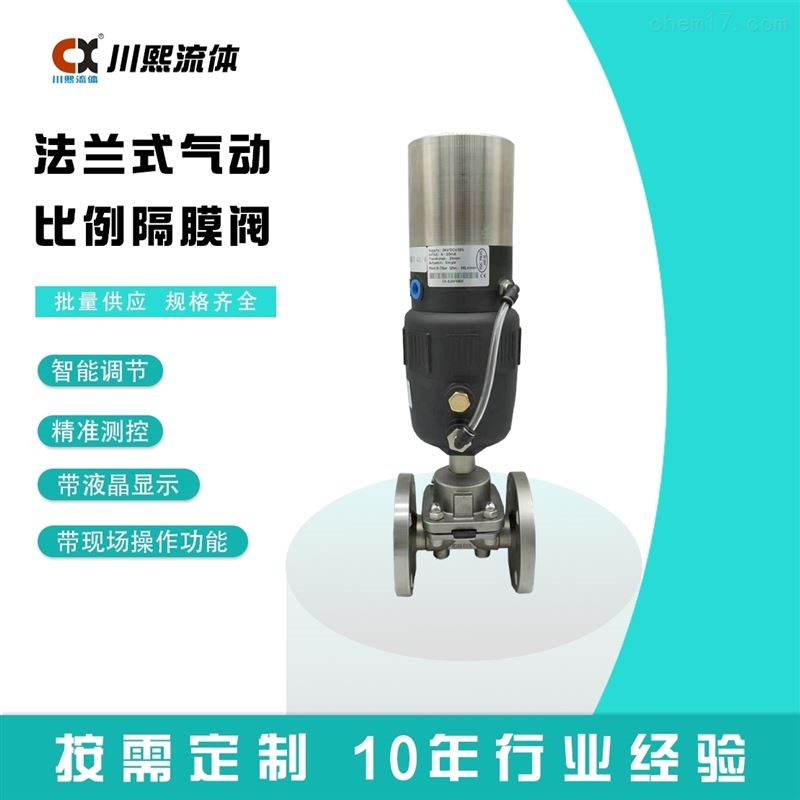
四、制造工艺与质量控制
高质量的制造工艺是确保调节阀可靠性的另一关键因素。精密的加工技术和严格的组装标准可以减少内部间隙,提升密封性能。在制造过程中,应严格控制材料的热处理工艺,确保其达到最佳的力学性能。同时,全面的质量管理体系,包括原材料检验、过程控制、成品测试等环节,是保证产品一致性和可靠性的基石。
五、智能监测与维护
随着工业4.0时代的到来,智能化成为提高设备可靠性的新途径。为该调节阀配备传感器和远程监控系统,实时监测阀门的工作状态,如温度、压力、振动等参数,可提前预警潜在故障,实现预防性维护。结合大数据分析,可以进一步优化操作策略,提升系统整体的稳定性和效率。
综上所述,气动蒸汽调节阀在高温高压环境下的可靠性研究是一个涉及材料科学、机械设计、制造工艺及信息技术等多学科交叉的复杂课题。通过选用耐高温高压材料、优化结构设计、实施严格的质量控制以及引入智能化技术,可以显著提升阀门在异常条件下的工作性能和寿命,保障工业生产的高效与安全。未来,随着新材料、新技术的不断涌现,气动蒸汽调节阀的可靠性和适应性将得到进一步提升,更好地服务于各种复杂工况下的工业应用。